Lean Six Sigma Consulting in New York
Contact Us
The Six Sigma Lean Method
Simply put, Lean Six Sigma Experts of New York supports companies through planning and consultation, to eliminate anomalies, inefficiencies in service, or mistakes. A control map with points relating to the service or process is often used in Lean Six Sigma. Registered products and activities must fall into one of many categories, as shown by the points on the table. Additionally, points that do exceed the specified limits are referred to as system glitches or defects.
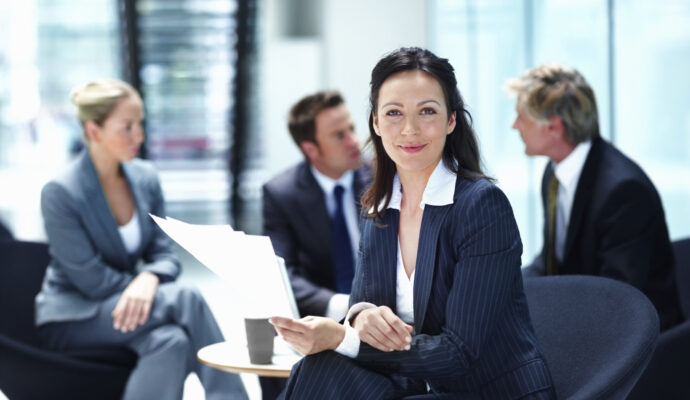
Reasons to Employ Lean Six Sigma Experts of New York
- Assists in the extension of your company’s strategy: Lean Six Sigma Experts of New York are vital to a company’s success. When a company defines its tasks, priorities, and performs SWOT analysis, Six Sigma approaches enable it to concentrate on areas for improvement more systematically and efficiently. Let’s take a look at a hypothetical situation and see what we think. If the industry’s target is to become a cost leader, Lean Six Sigma can boost yields, improve internal procedures, keep the lowest-priced sourcing options, and eliminate needless complexities.
- Keeps bosses and employees motivated: What is the secret to company success that all too many entrepreneurs and company owners overlook? That is the effectiveness of the employers and personnel. They lead to improved performance, which leads to increased service and revenue. Employees must therefore be inspired and guided to excel and perform effectively. Rapidly growing companies who engage with their employees see a 25 to 50 percent increase in productivity. Using Six Sigma problem-solving approaches and tools effectively fosters workforce growth and leads to the advancement of a business culture that promotes balanced knowledge-sharing and employee participation.
- Helps you significantly minimize turnaround times: Enterprise projects are notorious for missing deadlines. This is largely due to developments in the project scope as well as recent changes in management policies. Using Six Sigma methodology, you will form expert teams at all levels of the organization. Professionals are often chosen from a diverse set of functional disciplines. This unit is in charge of determining the causes that could jeopardize the project and cause it to be delayed for an extended period. This party would then be tasked with devising methods to mitigate the negative consequences of failure. Many prestigious brands have seen a 35% drop in cycle times since introducing Six Sigma.
Since choosing the correct Lean Six Sigma partner, vendor, or supplier is vital to success, it only makes sense for us to extend our experience to create a list of often asked questions to answer when assessing prospective business partners. Here are some of the most commonly asked questions, along with some tips about what to expect in terms of responses:
A Lean Six Sigma expert will work with you and your key colleagues within the company to form a cross-functional development team. The associate you choose should be an expert in education, processes, and execute best practices. Members of the organization should be well-versed in some of the more current project control methodologies for achieving revenue goals, as well as an appreciation of the company's broader marketing strategy and customer approach. This could be a red flag if the first phase of the startup project is entirely based on organizing training courses. Any Lean Six Sigma implementation in a company should start with a comprehensive understanding of the company's customer approach, as well as the internal change management and process optimization culture, and then move on to the creation of a plan that adapts the solution to those realities. Strategy evaluation is critical when applying Lean Six Sigma in the workplace. One of the most important facets of this process is breaking down conceptual focus areas into practical concepts. The project development process would aid in the identification and linkage of high-value, well-scoped projects to strategic goals, thus reducing project lead times and internal operational resource shortages. After identifying plans, main collaborators can be contacted to affirm tentative findings and prioritize programs. In addition to many Lean Six Sigma schemes, several initiatives that the company could address will be found. Project charters, which are written to provide a business basis for each project as well as to serve as a steering system for improvement activities, may be included as part of the startup process for selected Lean Six Sigma project proposals. Baseline benchmarks are often developed at this stage, enabling us to measure the success of projects and process improvements. The methods must be used regularly over time. Team members must be aware of their roles and responsibilities. Any team member must be judged separately in terms of the team's objectives. Similarly, Lean Six Sigma must be seen as a long-term strategy rather than a series of workplace steps; it is simply about the transition. The commitment of the project's leadership paves the way for the future. Rather than becoming a project, it is a matter of tradition and approach. It necessitates perseverance over time. The approach must be expressed in the organization’s plans and the organization itself. To measure outcomes, display graphs and figures are used. Recognize appropriate habits for today's environment. Reward the outcomes of the proposed program. Several people have told me, "We are a customer-driven company!" That's all well and good, but what distinguishes customer-driven companies from others? Customer-driven companies, on the other hand, are committed to providing high-quality products and services that meet or exceed their customers' needs. You enter a restaurant and place an order for a pie. What you anticipate and what you received demonstrates how well or poorly a company does. You are overjoyed that you get more than you anticipated. On the other hand, if there is a discrepancy in what you wanted and what you received, this might lead to dissatisfaction. We provide you with tools and a structure for identifying and evaluating the wishes and desires of your customers. This brings an end to discussions of "What Success Looks Like." What if we told you that "poor systems cause 95% of errors"? Errors are thus referred to as a "People Crisis" or "Human Mistakes" in many organizations. What are the ramifications? They attempt to help consumers by forcing them to use outdated systems. In a Lean Six Sigma industry, the focus is on production efficiency and lean processes. Attempts are made to improve systems to reduce errors. Routine tasks can be removed or simplified to reduce the need for human interaction. As a result, manual labor becomes less monotonous, allowing employees to focus on higher-value tasks. We also have many opportunities for staff to routinely learn various approaches. They will be able to teach others about the tactics and applications after integrating them into their units. Both of which lead to the advancement of one's career.
What Is The Standard Protocol For A New Client's Initial Setup?
What are your project selection and project startup procedure?
Is Lean Six Sigma A Set Of Improvement Initiatives?
How does it benefit the customer?
How Does It Benefit Employees?
There are so many areas or regions where we offer these services with most of them being cities.
However, if you need any of these services, you need to contact us. The list below comprises the areas where we offer these services.